Cerberus was born in Engineering Design II at Saint Mary's University as a competitor. Cerberus is designed to load, carry and deploy three probes on a terrain based course.
During this process, the robot was divided into three assemblies: chassis, arm and claw. Two concepts were developed for each. The four-wheel drive chassis was chosen for ground clearance. The single pivot extension arm was chosen for ease of operation and provides tangential movement of the claw. The triple pincer claw was chosen to reduce time required to traverse the course.
Cerberus is constructed from a standard course VEX kit with materials provided for fabrication of specialty parts.
Hand Sketches
Each component required two concepts. These concepts were developed as hand sketches which include mechanical operation, relationships between components and detailed descriptions.
Each member of the team was assigned a component to develop and sketch.
The concepts were compared assessing complexity, practicality and probability of success.

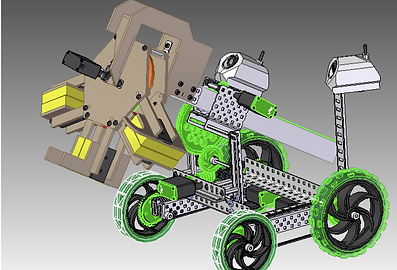
Computer Assisted Design
Solid Edge was used to create all parts used in Cerberus. Some of the sub-assemblies were first created in Solid Edge, such as the Claw Carrier. This allowed the team to assess the clearances required. These requirements actually shaped the front place of the carrier.
The sub-assemblies were created and then all were joined together bringing the Cerberus to life in the virtual domain.
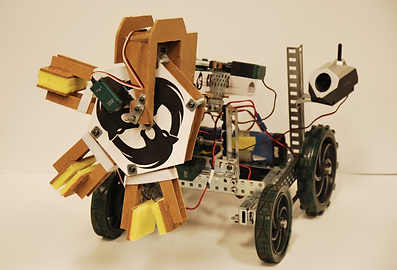
Prototype
Functional chassis prototypes were created for unpowered preliminary testing as part of the concept assessment process. As VEX kits provides the means for ease of assembly and modification, this was the optimal means to develop chassis designs.
The triple pincer claw was developed with a combination of sketches and prototypes constructed from foam core board. This provided a proof of concept for the mechanics behind the claw.